|
第6回 「製材の機械」
|
吉野中央木材(株)専務が送る、国産無垢材製材所のドキュメント。 |
もくじページへ戻る ┃ 「原木の皮むき」 ┃ 「木取りの基本」 |
|
1、“製材”とは一体!?
|
製材所のメインと言えば、やはり「製材」です。今回はその模様をお伝えしようと思います。ようやく本番といった感じです。 |
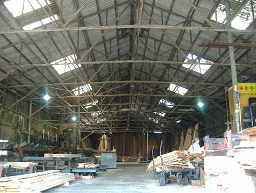 |
←■いざ製材所の内部へ…。 吉野中央木材(株)の心臓部ともいえる製材機が二座据えられている広い工場内の様子です。 事故防止のため足元は常に整頓されており、作業時は明るい照明を点しています。 |
|
まず「製材」とは一体どういう事でしょうか。 木材は主に建築資材に用いられます。柱・梁・土台などの構造材や床・天井などの内装材、扉・窓枠などの建具材など、建築資材を原木から作り出す作業を「製材」と呼びます。大昔は大工さんが“ちょうな”という手斧を使って、丸い原木を削って、柱などの角材を作っていたそうです。 これが製材の始まりという事になるのでしょうか。 その後、素材生産業を営む人(いわゆる林業家)が自分の山の木を製材し、建材として売るようになりました。 機械化される前まではやはり人力による製材だったようです。 |
さすがに“ちょうな”は弊社にありませんでしたので、似た雰囲気の道具ということで、これは皮むきのカマです。 “ちょうな”という手斧はこれよりも大きい感じです。■→ |
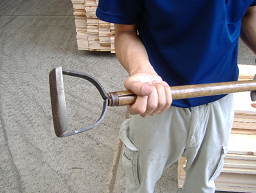 |
|
機械化のはじまりは、どうやら水車の動力を利用した装置のようです。 当時のノコギリの形状は現在主流の“帯ノコ”(帯状のノコギリ)ではなくて、“丸ノコ”(円形のノコギリ)で、回転方向に対して平行に原木を入れて挽いて行くスタイルだったようです。 この水車製材は静岡県の天竜が発祥の地のようで、なんと現在も行われている製材所さんがあるみたいです。聞き伝えなので、確かな情報ではないのですが…。 |
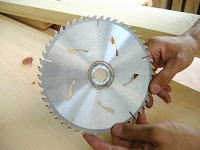 |
←■上が丸ノコ、下が帯ノコです。写真の丸ノコは小型のもので、 原木を挽く場合は直径70cm位の丸ノコを使っていたそうです。
その名が示すとおり、帯ノコには帯状になっており、6〜7mの長さがあります。■→ |
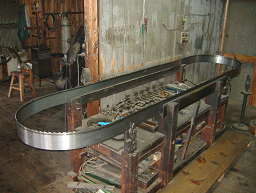 |
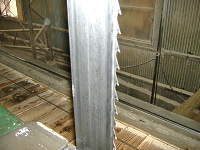 |
|
機械化に関しては、蒸気機関を利用したものもあったそうです。水車が先なのか、蒸気機関が先なのか。水車が先のような感じはするのですが…。 吉野は林業の歴史が古いので、昔は水車とか蒸気機関の製材もあったのだろうと思い、どちらが最初だったのかを調べてみたら、ちょっと意外な結果になりました。 ここ吉野は日本有数の林産地として知られ、その林業の歴史は室町時代にまで遡ります。500年近くの歴史があるのだから、色々な製材の形態があっただろうと思ったのですが、吉野で製材業が始まったのが昭和以降と比較的歴史が浅く、製材機械はすでに電力で動いていたそうです。元来吉野は素材生産と樽丸作り(樽丸とは酒樽の材料)が専門で、杉や桧は吉野川で和歌山まで流して出荷し、和歌山で製材が行われていたのでした。 吉野材の製材拠点が和歌山から奈良に移った理由の一つは、原木のままでは安く買い叩かれる場合が多く、原木に「製材」という付加価値をプラスしようという考え方です。昭和初期に有志が立ち上げた日本初の木材工業団地は、現在でも50軒近い製材所の集積地で、日々切磋琢磨をしています。 |
|
2、“送材車”付“帯ノコ盤”に迫る!
|
製材の話からちょっと脱線しました。製材所の内部に戻りましょう。
まず、最初に目に入るのが「送材車付帯ノコ盤」です。通称“台車”です。 主に原木を挽いたり、乾燥した角材を挽き直したりする製材機械で、これがないと製材が始まりません。 原木を「送材車」に固定し、回転する「帯ノコ盤」に通して、挽いて行く仕組みになっています。 |
番台に原木が載っています。 左奥に見える黄色いものが帯ノコ盤です。 原木に隠れてしまっていますが、中央の奥に送材車があります。 番台から送材車に、材を一本一本降ろして挽いていきます。■→ |
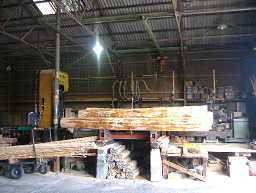 |
|
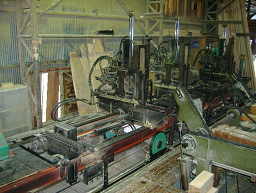 |
←■ちょっと解り難いですが、これが送材車です。 レールの上にトロッコのような感じで据えられています。 |
|
送材車の下のレールです。 送材車はこのレールの上を電車みたいに移動して、帯ノコ盤に材木を押し当てていきます。■→ |
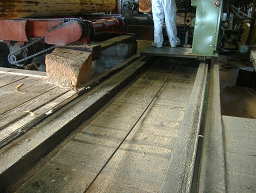 |
|
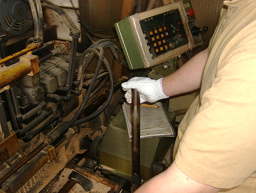 |
←■送材車の上の操縦席です。 オペレーターの握っているハンドルを倒すと前後進します。 この台車の細かな操作を、この操縦席から行います。 レトロなメカニカル感がかっこいいコクピットといった感じです。 |
|
これが帯ノコ盤です。帯ノコが高速回転をして、原木を挽いていきます。 製材業の主役機器ですが、かなりの危険も伴いますので、熟練のオペレーターが、しっかり操作する事が大切です。■→ |
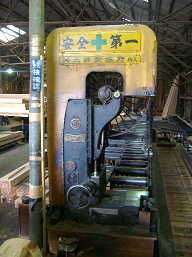 |
|
弊社には「送材車付帯ノコ盤」が3機あります。古いもので40年近く頑張る働き者もいます。 メンテナンスがしっかりしているので、現役バリバリで精度もバッチリです。 それぞれ特長というか、個性がありますので、それに応じて色んな部材を挽き分けています。 |
|
3、帯ノコ盤の仕組み
|
では最初に帯ノコ盤について見ていきましょう。 帯ノコ盤の仕組みは、上下の大きな円盤(ノコ車と呼びます)に帯ノコが固定され、高速回転するというものです。上下2ヶ所を支点とする為、安定度が非常に増します。 製材機械の主流が丸ノコから帯ノコに変わった理由はこのあたりにあると思います
。 丸ノコはその大きさに比例して、ノコ自体を安定させる為にノコを分厚くする必要があり、挽き道が大きくなってしまう欠点がありました。また、丸ノコは支点が円の中心の1ヶ所しかない為、安定度にも問題がありました。さらに、木材に接する面積割合が大きい為、摩擦係数が高く、丸ノコ自体が高温になり、歪んでくるという事もありました。 昔は回転する丸ノコに水を掛けながら製材をしたという逸話が残っているほどです。帯ノコの製造技術が確立されると、精度にも安定度にも優れる帯ノコが普及したというわけです。 |
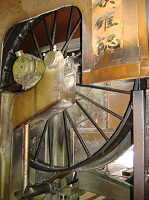 |
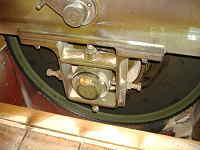 |
←■帯ノコ盤の上下についている円盤(ノコ車)です。ここに帯ノ コが付けられます。 |
|
この帯ノコはどうやってノコ車に固定されているのでしょうか。見た感じでは、帯ノコには固定する穴や止め金などはありません。帯ノコは3つの要素でノコ車に固定されています。 まず1つ目は上下のノコ車を機械の圧力で押し広げ、帯ノコを張ります。ですが、これだけでは原木を挽く時の圧力で、帯ノコが外れてしまう危険性があります。 そこで2つ目の要素。 それはノコ車の角度です。送材車の進行方向に対してノコ車の角度は垂直ではないのです。肉眼では分かりづらいのですが、ノコ車は手前に少し傾いています。こうする事によって、進行方向に対する負荷が帯ノコとノコ車にそのままストレートには掛かりません。 さらに3つ目の要素。実は帯ノコは円すい形状をしています。刃がついている側がほんの少しだけ狭くなっています。1mm程度のズレです。これで帯ノコがノコ車から押し出される危険性がほぼ消えました。 このズレはそれぞれの帯ノコ盤の性格・特徴によって変わります。弊社では工場内に目立工房を持っており、専門の職人さんが帯ノコの目立てを行い、ズレ幅の調整も行っております。この目立のお話は非常に深いので、また後ほど…。 |
吉野中央木材(株)目立工房の内部です。 最近ではコンピューター制御された機械による目立が大半ですが、弊社では職人さんが手作業で行っています。すごい職人芸です。■→ |
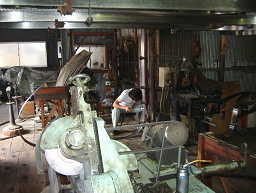 |
|
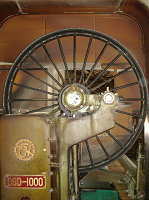 |
 |
←■帯ノコ盤のノコ車にもいくつか種類があり、このノコ車によっても製材の精度が変わってきます。 左の2種類の写真を見てください。ノコ車の形状の異なる二つの帯ノコ盤です。 左のノコ車はスポーク式、右のノコ車は鋼板式と呼びます。スポーク式に比べ、鋼板式の方がどっしりした感じがすると思います。鋼板式のノコ車は1枚板の鋼から作っているため、頑丈さが違います。負荷の大きい大径木を製材する時には、その違いが歴然になります。鋼板式の方がブレが少なく、精度の高い製材ができます。 |
|
ところで、昔は“帯ノコ”ではなく“丸ノコ”が主流だったと書きましたが、その当時は送材車もなく、原木をトロッコのようなものに固定して、人力で押して挽いていたそうです。僕の父親(弊社の社長です)が小学校の頃なので50年近く前、昭和30年代の話です。 その当時の製材風景から、原木を押す人を「ハラオシ」、受け取る人を「ハナトリ」と呼びました。お腹に原木を当てて押していたので、「腹で押す」が「ハラオシ」になり、原木の先、つまり「鼻」を取るから「ハナトリ」になったようです。(このコラムの元である「月刊杉web版」の連載タイトル「吉野杉をハラオシしよう!」は「ハラオシ=製材する」という所から名付けました。 |
|
4、送材車の仕組み
|
つづいては「送材車」について見て行きます。
丸太を挽く時に何も考えずにノコギリを入れてしまうと、最悪の場合には製品を何も取れずに終わってしまう場合もあります。 そこで必要になるのが「木取り」です。 1本の原木を出来るだけ無駄なく取れる事を「歩留まりが良い」と言い、製材をする時に心がける事のひとつです。どの方向にノコギリを入れていくかが重要で、木はまっすぐに見えても微妙に曲がっており、1本1本異なります。また取ろうとする製品の種類によってもノコギリに入れ方が変わってきます。 |
同じ杉でも1本1本性格が異なります。その見分けがプロの技。 “木取り”については、次回詳しく紹介させていただきます!■→ |
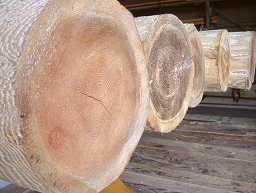 |
|
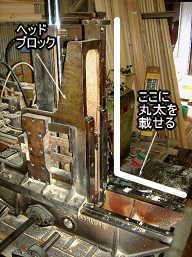 |
←■そこで“木取り”をしっかり行うために、送材車の登場になります。
送材車を手足のように操作し、原木の向きを調整して行きます。 送材車には「ヘッドブロック」と呼ばれる丸太を乗せる台座(右写真)が3機ついており、それぞれで丸太の元・中・末の三点を押したり引いたりして、帯ノコにどういう角度で丸太を押し当てて挽いていくか決定していきます。 |
|
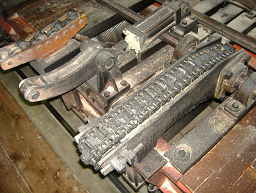 |
ヘッドブロックには「木廻し」というキャタピラ(左上写真)と、「木支え」というアーム(左下写真)が備えられていて、これらで丸太を挽く角度に固定して、3台の「ヘッドブロック」の1台ごとを微妙に調整しつつ、ノコギリを入れる方向を探ります。
実際には右写真のように丸太をコロコロ回しながら、ノコ道を探っていきます。 これがまたまた難しい!
※写真にポインタを置いてください。 |
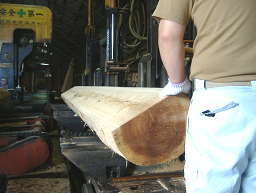 |
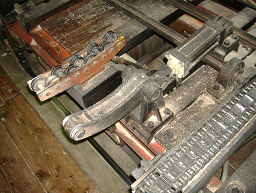 |
|
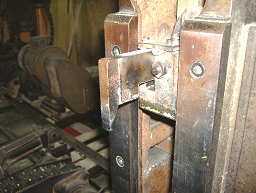 |
←■さて、ノコギリを入れる方向が決まりました。 送材車を前進させ、高速回転している帯ノコに丸太を押し当て挽いて行きます。 その時に原木を固定するのがヘッドブロック上部についている、この「カスガイ」です。 このカスガイを丸太に食い込ませて、がっちり動かないように固定して、挽いて行きます。 途中で丸太が外れると非常に危険! 絶対確認次項です! |
|
原木を挽く送材車付帯ノコ盤は進化を続け、ツインソー(twin saw)という帯ノコ盤も登場しました。これは帯ノコ盤が2台並んでおり、その間に原木を通すもので、さらに帯ノコの両端に刃がついており、行き戻りで原木を挽くことができるので、効率性がアップします。またコンピューター制御で無人で製材をする機械も登場しました。 ですが、これらの製材機械は一等材(節あり材、一番下の等級です)の製品を挽くのには適していますが、ここ吉野のように一等材だけでなく、化粧材も主力としている所では、やはり人間の目で見ながら1本1本の原木を丁寧に製材する以外に手段はありません。 このあたりが吉野材のコストを引き上げる要因になっているのかもしれませんが、これが吉野材の特徴でもあるわけで、この辺りにも難しい問題があるように思います。 しかし、あまり期待していなかった原木から見事な無節の材が取れたり、最高の原木から節やハチクイが出たり…と、「製材」というものは自然を相手している
ので非常に難しくもあり、楽しくもあります。 |
|
さて、次回はこの製材の面白さをお伝えすべく、実際に「木取り」の模様を現場リポートしてみたいと思います。 お楽しみに! つづく
|
|
もくじページへ戻る ┃ 「原木の皮むき」 ┃ 「木取りの基本」 |
|