|
第8回 「帯ノコの目立て術」
|
吉野中央木材(株)専務が送る、国産無垢材製材所のドキュメント。 |
もくじページへ戻る ┃ 「木取りの基本」 ┃ 「木材の乾燥」 |
|
1、“目立て”とは…?
|
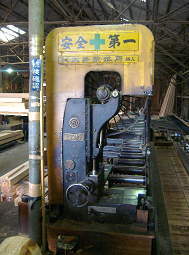 |
今回は製材には欠かせない“帯ノコ”に再びスポットライトを当てようと思います。
帯ノコについては第6回にてご紹介をさせて頂きましたが、今回は帯ノコの「目立て」の世界を見ていきましょう。
←■帯ノコ盤です。
帯ノコが高速回転し、製材を行います。 |
|
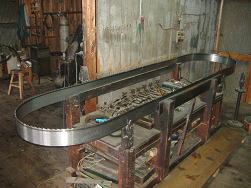 |
大工さんがカンナを研いだりするように、製材する時によく切れるように“帯ノコ”を調整する事を「目立て」と言います。帯ノコをよく切れるように目立てをしておかなければ、製材の精度が低下するだけでなく、帯ノコが割れるなどの危険もあり、製材には欠かせない役割の一つです。
←■製材機から外した状態の帯ノコです。 その名のとおり帯状になったノコギリです。 詳しくは第6回へどうぞ! |
|
目立ては“勘や経験”という職人技的な部分が多く、現在では手作業で目立てを行える人は少なくなったようです。昔はどの製材所にも目立て工房があり、専任の職人さんが帯ノコを1枚ごとに手で触れながら、目立てを行っていたそうです。現在では分業化が進み、コンピューター制御された機械が自動的に目立てを行うのが主流になりました。ですが、帯ノコ盤は1台ごとに特性があり、またハラオシ(製材操作者)の挽き方にも個性があり、均一的な目立てでは対応しきれない部分があります。それぞれに合った目立てを行う事は精度を上げ、作業効率を向上させるわけです。また、製材から戻ってきた帯ノコを見て、製材機の不調を察知する事もあり、これはコンピューター制御された目立てでは成し得ない技だと思います。 |
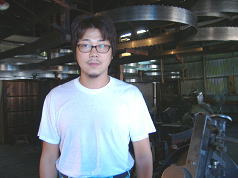 |
弊社吉野中央木材では自社内の工房にて、現在も専門の職人さんが目立てを行っています。
今回はその内部をご紹介し、その職人芸をご覧頂こうと思います。まずは目立て職人をご紹介しましょう。 弊社で目立てを担当しているのが、大石一也さん、今年37歳です。 職人という事からものすごい高齢の熟練工を想像されたかもしれませんが、ナイスガイな職人です。
←■目立て担当の大石さん。
|
|
|
2、目立ての手順
|
それでは、目立ての様子を見て行くことにしましょう。
まずは目立て工房の内部へ……。
工房内は沢山の帯ノコが吊り下げられていて、いつでも取り替えれるよう、このように簡単かつ安全に保管されています。
“目立て場”には、かなり古い物ですが、使い込まれた道具や器械がとても丁寧に整理整頓され、すべてが未だ現役で稼動していることが伺えます。 それらを一見しただけでも、受け継がれてきた職人技術と気質を感じさせられます。 |
|
2−1、歪みの補正
|
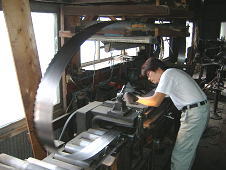 |
まず、帯ノコの「歪み」を確認します。
帯ノコは“帯状”のノコギリですから、この帯に歪みがあると帯ノコの回転軸がぶれてしまい、製材精度が落ちてしまいます。
←■このようjに帯ノコを回転させながら見て行きます。 |
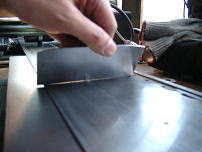 |
帯ノコを水平な台に乗せて、まずは歪みを確認していきます。
←■手に持っている金定規との間に見える隙間が歪みです。 |
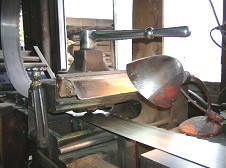 |
帯ノコはプレス機の中を通っています。 プレス機内のローラーで歪みを補正します。圧力の度合いで歪みがさらに広がってしまう可能性があるので、注意深く調整していきます。 |
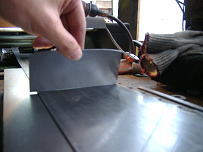 |
←■歪みが規定値以下までとれて、ぴったりと金定規が当っています。 |
|
|
2−2、ヒートテンションと腰
|
次に帯ノコに「ヒートテンション」と「腰」を入れます。
「ヒートテンション」とは帯ノコの刃の下部あたりを加熱する事です。 こうする事で、帯ノコの刃がついている側が少し縮み、帯ノコは円すい形状に変形します。これは第6回でお伝えしたように、帯ノコ盤の上下のタイヤから外れないようにする為の一つの要素になります。 |
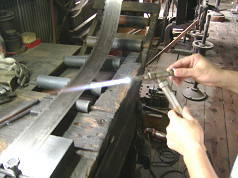 |
←■バーナーで加熱して行きます。バーナーの炎は3000度近くです。 |
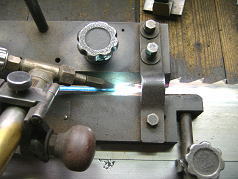 |
←■バーナーを固定し、帯ノコを低速で動かします。 帯ノコは約500度まで熱せられます。 |
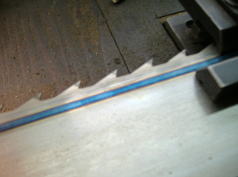 |
←■青黒い色合いになり、ヒートテンションが入りました。 |
|
「ヒートテンション」を入れる時の温度調整や、帯ノコを移動させるスピード調整によって、ヒートテンションの強さを調整しています。また「腰」を入れる時のプレスの強さによって、腰の強さを調整しています。 それぞれの帯ノコ盤に応じて、強さを微妙に調整しているわけです。まさに職人芸です。 帯ノコは高速回転しながら、木材を挽いて行きますので、摩擦熱が発生します。この熱で帯ノコが緩んでくるので、摩擦熱の具合も考慮して腰を入れなければなりません。 |
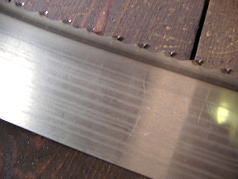 |
続いて、「腰」を入れていきます。
帯ノコのお腹の部分をプレスして、腰を作ります。5ミリ幅の筋を10本ほど付けます。
←■帯ノコのお腹の部分に白い筋が付きました。これが腰です。 |
|
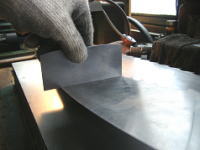 |
昔はヒートテンションという考え方がなく、現在ヒートテンションを入れている部分もプレスで腰を入れていました。プレス圧を調整して、円すい形状にしていたそうです。しかし、この方法だとプレス圧を調整したとしても、大きな差を出すことは難しく、腰の“持ち”が良くなかったそうです。 バーナーによって焼き付ける事でメリハリが付き、“持ち”が格段に進歩しました。
←■上写真は、まだ「腰」を入れてない状態です。
下写真は「腰」が入りました。 帯ノコの両端で帯ノコ盤のタイヤに固定する感じです。 |
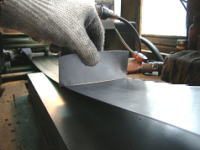 |
|
|
2−3、刃の掃除
|
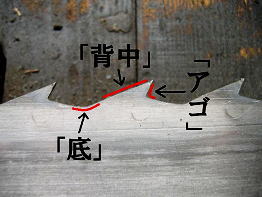 |
続いて、刃の“掃除”を行います。
まず刃の形状をご説明しましょう。刃には「アサリ」「アゴ」「底」「背中」と呼ばれる部分があります。「アサリ」と呼ばれる先端の部分で木材を挽いていくイメージになります。このアサリについては、次の工程でお話をするとして、ここではアゴ、底、背中の掃除についてご説明しましょう。
←■刃の各部の名称です。アサリは刃の先端部分に作ります。 |
|
アゴ、底、背中には製材時に“木粉”が付着します。この木粉が溜まりすぎると摩擦係数が高くなり、表面硬化を起こしやすくなります。 これは割れの原因となり、製材中に帯ノコが割れてしまうと非常に危険なため、十分に注意しなければなりません。 では、掃除の様子をご覧ください。 |
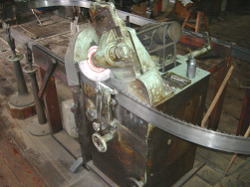 |
←■これが掃除をするのに使われる「目立て機」と呼ばれるものです。
※ポインタを写真に置いてみてください。 |
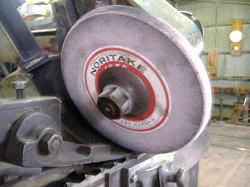 |
←■目立て機には円盤状の砥石がついています。 |
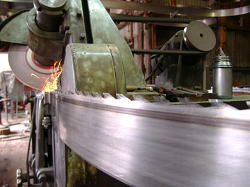 |
←■円盤砥石が回転し、刃の掃除をして行きます。この時の砥石の当て方の調整が難しく、強く当てすぎると帯ノコが焼けてしまいます。
機械が帯ノコを少しずつ動かし、一枚の刃ごとに擦って行きます。
※ポインタを写真に置いてみてください。 |
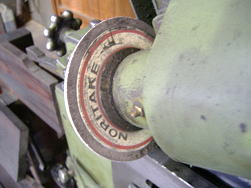 |
←■円盤砥石は約2ヶ月でほとんど無くなってしまいます。 |
|
|
2−4、アサリ
|
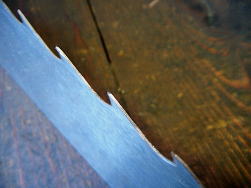 |
続いて、「アサリ」を作る工程に移ります。帯ノコの目立ての中で最も重要な工程です。
そもそもアサリとは何でしょうか? アサリとは刃先の部分のことで、耳かきの先のような形状をしています。製材をする時に木を切りかく部分です。 新品の帯ノコにはアサリはついておらず、目立てをする時に作ります。“スウェージ”というペンチみたいな道具を利用して、刃先を平べったく潰すような感じになります。 1本の帯ノコには約240個の刃が付いており、この全てにアサリを付けます。
←■帯ノコを刃の部分です。上写真ははアサリをつける前、下写真がアサリをつけた後です。耳かきの先のような形状をしています。
|
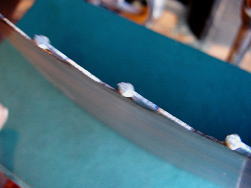 |
|
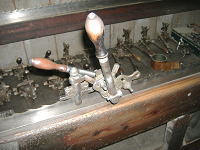 |
←■これが“スウェージ”です。
帯ノコの厚みは約0.9ミリですが、このアサリは約1.7ミリあります。大きすぎても小さすぎてもダメなので、スウェージの力の入れ具合が非常に難しいです。スウェージ自体の調整も難しいので、アサリ付けは目立て職人の腕の見せ所です。
←■こんな感じで使います。 |
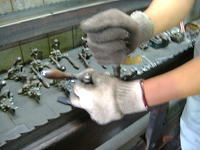 |
|
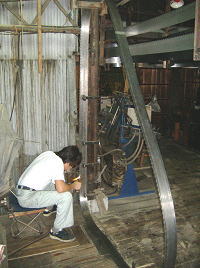 |
そして、このアサリに“ステライト”という金属を溶着させます。そのままのアサリでも製材は可能ですが、ステライトを付ける事で剛性が高まります。 ステライトは他の金属に比べて熱を加えても耐性が落ちないという特徴があり、これを850度の熱で溶かして、アサリに溶着させます。 これぞ職人芸!といった感じです。
←■帯ノコを縦に設置し、アサリ一つずつにステライトを溶着させます。 |
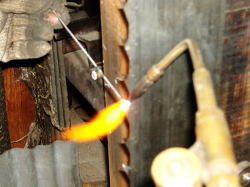 |
←■棒状のステライトの先を約850度の熱で溶かしながら、アサリに付けます。帯ノコとステライトの溶解熱が近い為、アサリ自体を溶かしてしまう恐れがあり、非常に難しい作業です。 |
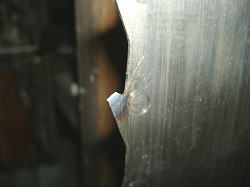 |
アサリにステライトを溶着させた時点では、刃はもろく折れやすい状態になっています。そこで「焼き戻し」を行います。
←■カナヅチで叩くと簡単に折れてしまいます。 |
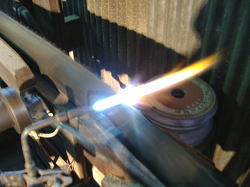 |
焼き戻しとは、溶着時の850度の半分くらいの熱で再度炙る事をいいます。 先ほど掃除を行った“目立て機”に帯ノコをセットし、バーナーで刃先を熱します。焼き戻しを行う事で、刃に柔軟性が生まれ、耐性が高まります。
←■約450度の炎で再加熱します。 |
|
|
2−5、研磨
|
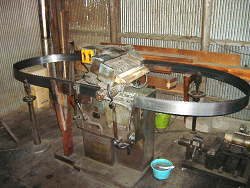 |
焼き戻しを終えると、最終工程の研磨に移ります。
この段階ではアサリの幅が広いので、アサリの両サイドを研磨します。「サイド研磨機」を利用します。
←■サイド研磨機です。右の写真は砥石部分です。 |
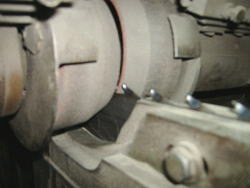 |
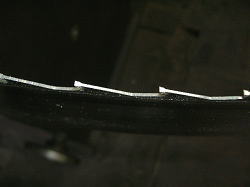 |
←■アサリの両サイドが綺麗に研磨されました。この状態を「バチアサリ」と言います。
サイド研磨を終えると、先ほど掃除を行った「目立て機」にて最終仕上げの研磨を行い、目立て完成です。長い工程でした。 |
|
|
3、職人芸
|
文面ではその難しさが上手く伝えられず、それぞれの工程は簡単そうに感じるのですが、実際に目立ての現場を目の当たりにすると、非常に繊細な技の連続です。目立て担当の大石さんの見事な職人芸と言うより他ありません。 しかし、この技は一朝一夕で成し得たものではありません。
目立て担当の大石さんが入社したのは13年前。 その当時、弊社には凄腕の目立て職人さんが活躍していました。奈良県でも指折りの名人だったそうです。しかし名人は定年間近で、後継者の育成が急務になりました。
大石さんの話では、いとも簡単に目立てを行う名人を見て、「すぐに出来るようになる」と気楽に思ったそうですが、実際やってみると全然うまく出来なかったそうです。
当時大石さんは製材の方の仕事も担当していたので、毎日夕方から1時間、名人の講義を受け、講義後も夜の工場に残り、目立ての練習をしたそうです。 名人からは怒られ続け、イヤになった時もあったそうですが、1年間耐え続け、名人から「もう明日から一人でやってもええ。」と言われた時は、涙が出るほど嬉しかったそうです。 努力と根性が、その職人芸を築いたのです。
真夏の目立て工房の中は連日40度超え。大型扇風機は欠かせません。■→ |
|
今回は製材所の内部の本当にディープな世界をのぞいてみました。
次回は、製材所にとっては永遠のテーマとも言える「木材の乾燥」について考えてみたいと思います。お楽しみに! つづく
|
|
もくじページへ戻る ┃ 「木取りの基本」 ┃ 「木材の乾燥」 |
|